Француски институт за соларну енергију ИНЕС развио је нове ПВ модуле са термопластом и природним влакнима из Европе, као што су лан и базалт.Научници имају за циљ да смање утицај на животну средину и тежину соларних панела, уз побољшање рециклаже.
Рециклирани стаклени панел на предњој страни и ланени композит на задњој страни
Слика: ГД
Из пв магазина Француска
Истраживачи француског Националног института за соларну енергију (ИНЕС) – одељења француске комисије за алтернативну енергију и атомску енергију (ЦЕА) – развијају соларне модуле који садрже нове материјале на бази биологије на предњој и задњој страни.
„Пошто су угљенични отисак и анализа животног циклуса сада постали суштински критеријуми у избору фотонапонских панела, набавка материјала ће постати кључни елемент у Европи у наредних неколико година“, рекао је Анис Фоуини, директор ЦЕА-ИНЕС-а. , у интервјуу за пв магазин Франце.
Ауде Дерриер, координаторка истраживачког пројекта, рекла је да су њене колеге погледале различите материјале који већ постоје, како би пронашли онај који би могао да омогући произвођачима модула да производе панеле који побољшавају перформансе, издржљивост и цену, док истовремено смањују утицај на животну средину.Први демонстратор се састоји од хетероспојних (ХТЈ) соларних ћелија интегрисаних у потпуно композитни материјал.
„Предња страна је направљена од полимера испуњеног фибергласом, који обезбеђује транспарентност“, рекао је Дерриер.„Задња страна је направљена од композита на бази термопласта у који је интегрисано ткање два влакна, лана и базалта, што ће обезбедити механичку чврстоћу, али и бољу отпорност на влагу.
Лан долази из северне Француске, где је већ присутан цео индустријски екосистем.Базалт се налази на другим местима у Европи и плете га индустријски партнер ИНЕС-а.Ово је смањило угљенични отисак за 75 грама ЦО2 по вату, у поређењу са референтним модулом исте снаге.Тежина је такође оптимизована и износи мање од 5 килограма по квадратном метру.
„Овај модул је усмерен на кровну ПВ и интеграцију зграда“, рекао је Дерриер.„Предност је што је природно црне боје, без потребе за позадином.Што се тиче рециклаже, захваљујући термопластици, која се може претопити, одвајање слојева је такође технички једноставније.”
Модул се може направити без прилагођавања текућих процеса.Деријер је рекао да је идеја да се технологија пренесе на произвођаче, без додатних улагања.
„Једини императив је имати замрзиваче за складиштење материјала, а не да се започне процес умрежавања смоле, али већина произвођача данас користи препрег и већ је опремљена за то“, рекла је она.
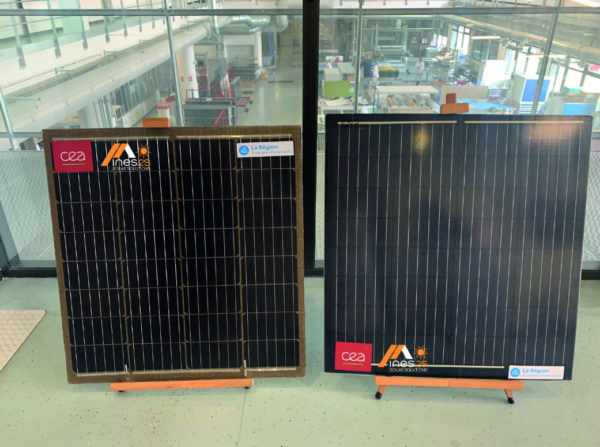
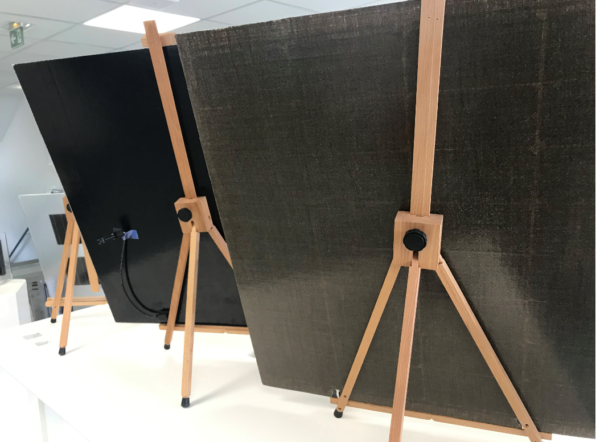
„Радили смо на другом животном веку стакла и развили модул састављен од поново коришћеног стакла од 2,8 мм које потиче од старог модула“, рекао је Дерриер.„Такође смо користили термопластични капсулант који не захтева унакрсно повезивање, који ће се стога лако рециклирати, и термопластични композит са ланеним влакнима за отпорност.
Задња страна модула без базалта има природну ланену боју, што би, на пример, могло бити естетски интересантно за архитекте у смислу интеграције фасаде.Поред тога, ИНЕС алатка за прорачун је показала смањење угљичног отиска за 10%.
„Сада је императив довести у питање фотонапонске ланце снабдевања“, рекао је Јоуини.„Уз помоћ региона Рона-Алпи у оквиру Међународног развојног плана, кренули смо у потрагу за играчима изван соларног сектора како бисмо пронашли нове термопласте и нова влакна.Размишљали смо и о тренутном процесу ламинације, који је енергетски интензиван.
Између фазе притиска, пресовања и хлађења, ламинација обично траје између 30 и 35 минута, са радном температуром од око 150 Ц до 160 Ц.
„Али за модуле који све више укључују еколошки дизајниране материјале, неопходно је трансформисати термопластику на око 200 Ц до 250 Ц, знајући да је ХТЈ технологија осетљива на топлоту и не сме да пређе 200 Ц“, рекао је Деррије.
Истраживачки институт се удружује са специјалистом за индукциону термокомпресију Роцтоол са седиштем у Француској, како би смањио време циклуса и направио облике у складу са потребама купаца.Заједно су развили модул са задњом страном направљеном од термопластичног композита типа полипропилена, у који су интегрисана рециклирана угљенична влакна.Предња страна је израђена од термопласта и фибергласа.
„Роцтоол-ов индукциони термокомпресиони процес омогућава брзо загревање две предње и задње плоче, без потребе да се достигне 200 Ц у језгру ХТЈ ћелија“, рекао је Дерриер.
Компанија тврди да је инвестиција мања и да би процес могао да постигне циклус од само неколико минута, уз коришћење мање енергије.Технологија је намењена произвођачима композита, како би им пружила могућност производње делова различитих облика и величина, уз интегрисање лакших и издржљивијих материјала.
Време поста: 24.06.2022